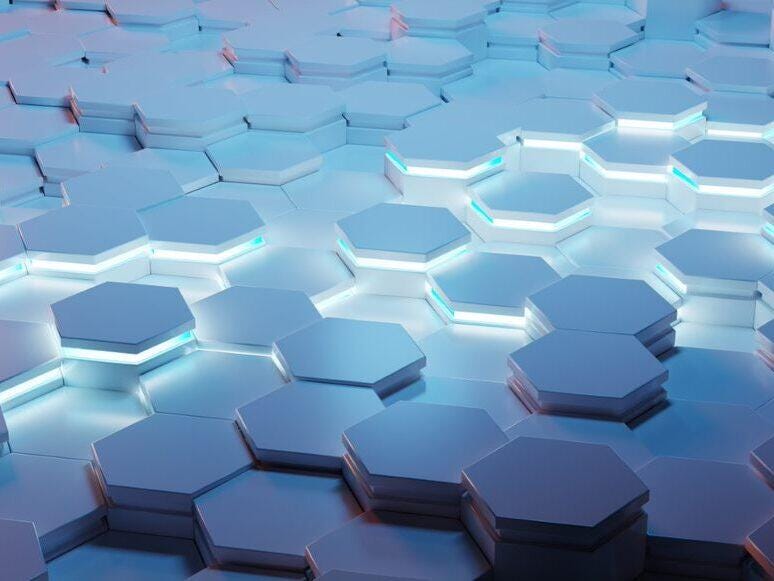
The Digital Edge of the New Cool
REMI DICKES, MANAGER APPLICATION ENGINEERING WITH COPELAND
DIGITALIZATION
“We developed perfectly matched components to achieve a very good value proposition using digitalization.”
The innovative Copeland CO₂ scroll solution for transcritical booster systems is not only based on a vastly improved technology thus allowing for a radically simplified architecture for CO₂ cooling circuits. The concept also includes the end-to-end digitalization of system components, resulting in far-reaching opportunities to further increase efficiency, reliability, and peace of mind. In this interview, Rémi Dickes, Manager Application Engineering with Copeland, explains the implications and benefits for customers.
The new Copeland scroll compressors for transcritical CO₂ systems combine several new and smart technologies to proliferate the natural refrigerant in all world regions. What role does digitalization play in this?
It is at the very core. The objective of digitalization is to provide our customers with system solutions that can be operated, monitored, and maintained at the highest reliability and efficiency level in a quick, simple, and productive way. Digitalization is supposed to ease our customers’ lives and therefore becoming key to all future developments. It is a means to record, analyze and evaluate data of the components and system operations based on which measures for improving system efficiency will be taken. As a manufacturer with a broad and diverse portfolio of products and solutions we are in a unique position: We design and manufacture the components while at the same time we develop the controls and algorithms used to turn data into actionable information. We own and manage all key functions, intelligence, and skills to realize digitalization and its purpose: to further improve our customers’ cooling systems and hence help them achieve their business goals.
How did you take digitalization into account in the CO₂ scroll solution’s development process?
We have a lot of experience with solutions that feature strong electronic components and data use. In our CO₂ program, we identified components ideally suited to achieve a very good value proposition using digitalization. This is particularly important since CO₂ adds to the complexity of the refrigeration cycle due to its properties. Consequently, we not only deliver a complete package of carefully pre-selected components that have been thoroughly tested, but also employ targeted digitalization to ensure they interact and communicate smoothly and reliably with each other, ultimately facilitating CO₂ deployment.
What are your digital solutions focusing on – system control, monitoring and diagnostics or maintenance?
There is definitely a focus on control, as we offer the CO₂ solution with a very advanced system controller. For monitoring, we have made sure our controllers are compatible and interoperable and can also connect to different monitoring systems in the market. In the field of diagnostics and maintenance we already have very advanced algorithms and will keep evolving them, like we do for all our platforms.
How does this system controller contribute to the overall goal of reliability?
The controller is digitally connected to the compressor drive, sensors, and other components and can communicate with other built-in management systems as well as with external networks. If for instance there is an issue with the compressor drive, the controller can initiate a reset of the compressor drive – and if the problem persists, make appropriate decisions to ensure the system’s reliability and continued operation even if there is a fault at one component. That kind of smart communication and data sharing is one of digitalization’s big advantages. It also helps to avoid costly false diagnoses, for example with the compressor: In practice, it turns out that alleged compressor damages often are not caused by the compressor at all, but by some other failed component that simply could not be localized. To avoid this, we use digitalization in a targeted manner. By properly recording the system operation and by using dedicated algorithms, our controller helps to identify the root cause of abnormal operation and to prevent erroneous diagnostics.
When you speak of communicating and data sharing, does that include IoT and Edge computing capabilities?
Yes, we are IoT-ready and provide data in an open, non-proprietary way. In this context, we differentiate between data that needs to be processed locally via Edge computing and data that can be outsourced to the cloud. System control data, for example, needs to be available very quickly, so there is no point in outsourcing it to the cloud. Selected data for KPI evaluation, on the other hand, can very much be moved to the cloud. And since different capacities such as the service manager or contractor have a different focus on the data, we enable our customers to use dedicated dashboards that filter out just the individually relevant information to gain meaningful insights.
What is the most important benefit that digitalization and its application in your CO₂ scroll solutions will bring to retail refrigeration?
Digitalization cannot be reduced to a single advantage; it opens up a wealth of important benefits and opportunities for all market participants. On the one hand, it enables our customers to further increase their systems' operational reliability, because the data obtained in actual operation can be used to tailor the respective product even better to their specific needs through runtime optimization. Secondly, customers can use the data provided by our solutions to monitor and evaluate their overall system performance even more precisely, for example in terms of energy efficiency. And thirdly, it provides us with important feedback that we can incorporate into product development – ultimately resulting in additional customer benefits.